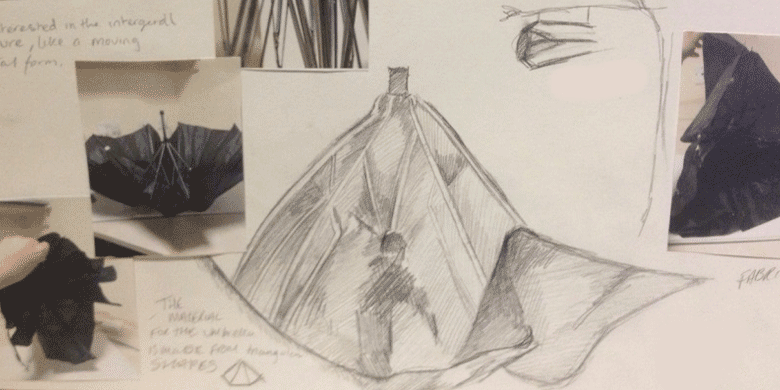
12 September, 2023
Making An Umbrella Come To Life
Promotional umbrellas, carrying logos and brand messages, serve as essential marketing tools for businesses worldwide. But how exactly do they come to life? Let's take a behind-the-scenes look at the entire manufacturing process, including material selection, printing methods, and quality control.
I. Conceptualisation and Design
A. Identifying the Purpose
Understanding your target audience and the intended use of the umbrella is crucial. Is it for a corporate event, a product launch, or a general marketing campaign? By defining the purpose, manufacturers can make more informed decisions about design, materials, and overall aesthetics, ensuring the final product resonates with the desired audience.
B. Designing the Artwork
The design phase goes beyond simply placing a logo on an umbrella. It's about crafting an engaging visual experience that aligns with the brand's identity. Designers must consider colour schemes, logo placement, text font, and overall balance. Mock-ups and digital simulations are often created to visualise the final product, and adjustments are made until the design is perfected. Remember the balance of an umbrella. You should either print a single panel, opposing panels or every other panel (assuming it is an 8 panel umbrella).
II. Material Selection
A. Choosing the Fabric
The fabric selection depends on factors such as durability, cost, and appearance. While polyester is known for its affordability, nylon might be chosen for its tear resistance, and Pongee for its sleek look. Material choice is aligned with the umbrella's purpose and the brand's image, balancing quality and budget constraints.
B. Frame Material
The umbrella's frame gives it structure and determines its functionality. Steel offers strength but may be heavier, fibreglass is known for its flexibility, and aluminium provides a lightweight option. The selection process involves analysing the intended use and desired characteristics, such as whether the umbrella must withstand heavy winds. In that case you would want to opt for fibreglass as it bends in the wind and returns to its original shape. Steel might be stronger, but once bent from a high wind it becomes very weak and is hard to put back to its former shape.
III. Printing Methods
A. Screen Printing
Screen printing is a popular method for simple designs with limited colours. It's cost-effective for large batches and provides a vibrant print. However, it can be less suitable for intricate patterns as the stencil needs to be manually created for each colour.
B. Digital Printing Or Transfers
Digital printing or transfers are often the method of choice for complex and multi-coloured designs. It prints the digital image directly onto the fabric or a transfer that is applied to the fabric, allowing for high precision and unlimited colour variations. Although it might be costlier, especially for small quantities, its quality and flexibility often justify the expense. Also, once you start getting into multiple colour prints, it can sometimes work out cheaper than screenprinting due to there only being one set-up cost, whereas screen printing, there is a cost for every colour printed.
C. Sublimation Printing
Sublimation printing uses heat to transfer dye onto the fabric, resulting in a durable, fade-resistant print. It’s an excellent choice for intricate and full-colour designs and provides a print that feels smooth to the touch, ensuring that the umbrella maintains its texture.
IV. Cutting and Sewing
The fabric is cut into the desired shape using machines that can either be automated for precision or manually operated for more unique shapes. Once cut, the fabric is sewn together to seams, alignments, and overall finish. This stage requires that the canopy aligns perfectly with the frame.
V. Assembling the Frame
The materials are fashioned into the ribs, shaft, handle, and other umbrella frame components. Each part must be carefully crafted and assembled to provide a seamless operation. The right connections and joints are essential to create a robust and durable umbrella. Here's an in-depth look at each part:
A. Ribs and Stretchers
The ribs and stretchers are the supporting skeleton of the umbrella, giving it its shape and allowing it to open and close smoothly.
- Material Selection: Often made of steel, fibreglass, or aluminium, the choice of material depends on the desired flexibility, strength, and weight.
- Shaping: The ribs and stretchers are shaped through bending or moulding processes to achieve the required curvature and length.
- Connection Points: The ribs are attached to stretchers using joints or rivets, allowing them to expand and contract as the umbrella opens and closes.
- Shaft: The shaft is the central support pole of the umbrella, connecting the handle to the canopy and housing the mechanism that allows the umbrella to open and close.
B. Material Selection: The shaft may be made from metal, wood, or composite materials. Metal shafts often undergo a coating process to prevent rusting.
- Length and Diameter: The shaft must be carefully cut and shaped to the desired length and diameter to match the overall size of the umbrella.
- Integrating Mechanism: The internal opening mechanism, often a spring-loaded system, is inserted into the shaft. This mechanism needs to be calibrated for smooth operation.
- Handle: The handle is where the user grips the umbrella, and its design can vary greatly in terms of material, shape, and style.
- Material Selection: Handles can be made from plastic, metal, wood, or other materials. The material often complements the overall design of the umbrella.
- Shaping and Finishing: The handle is shaped through moulding or carving to fit comfortably in the user's hand. Finishing processes add colour or texture.
- Attachment to Shaft: The handle is securely attached to the shaft using adhesives, screws, or other fastening methods, ensuring a firm and comfortable grip.
C. Connecting the Components: The final assembly involves connecting the ribs, stretchers, shaft, and handle to form a complete and functional frame.
- Ribs to Shaft: The ribs are attached to a top cap or runner that slides along the shaft, enabling the opening and closing of the umbrella.
- Quality Control: Once assembled, the frame's functionality is tested to ensure all parts operate seamlessly, and necessary adjustments are made.
The frame of an umbrella requires attention to detail, material expertise, and engineering precision. Each component must be carefully integrated to provide seamless operation, robustness, and durability. From the handle to the efficiency of the opening mechanism, every element plays a role in creating a functional and high-quality umbrella.
VI. Attaching the Canopy
The canopy is attached to the frame. This stage involves not only aligning the fabric with the skeleton of the umbrella but also ensuring that the canopy's tension is evenly distributed. This attachment ensures the umbrella opens and closes smoothly, providing optimal coverage and function.
VII. Quality Control
A. Inspection
A thorough inspection is conducted on each umbrella, checking for any materials, printing, or assembly defects. This involves both visual checks and manual assessments to ensure that all parts are properly aligned, the printing is flawless, and the materials meet the required standards.
B. Testing
Functionality tests are performed to assess the umbrella's overall stability, wind resistance, and operational mechanics, such as opening and closing. Machines or manual methods may be used to simulate different conditions, ensuring that the umbrella will perform as expected in real-world scenarios.
C. Packaging
Once the umbrellas pass all quality checks, they are carefully packaged to prevent damage during shipping. Packaging also presents an opportunity for branding, as companies can choose custom boxes or wrapping that reflects their brand identity.
VIII. Shipping and Distribution
The final step is shipping the promotional umbrellas to distributors or directly to customers. This involves selecting appropriate shipping methods, tracking the delivery process, and ensuring the umbrellas arrive in perfect condition. Customer satisfaction at this stage solidifies the success of the entire manufacturing process.
Conclusion
The production of promotional umbrellas is indeed a complex journey that requires precision, creativity, and coordination across various stages. From the initial concept to the final delivery, each step is interdependent and crucial in crafting a product that serves as a practical tool and a compelling marketing asset.
The Umbrellas Only Team